To bio ... or not to bio?
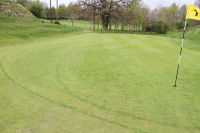
Biodegradable fluids as alternative to petroleum-based fluids
During the past two decades, the manufacturers and blenders of lubricants have been very busy developing eco-friendly, readily biodegradable and non-toxic fluids, as they estimate that 70% to 80% of hydraulic fluids leave systems they are working in through leaks, spills, hose breakages and fitting failures.
Biodegradable hydraulic fluids nowadays are high-performance products with environment-friendly properties. Unfortunately, many equipment end-users underestimate their performance and eco-friendly properties or regard their use as uneconomical. Within this article, I would like to address some of these preconceptions.
What is Biodegradability?
So, what is Biodegradability? It is defined as the ability of a substance to be digested or consumed by naturally occurring microorganisms or their enzymes, present in water, air and soil systems, and be converted to inorganic substances, such as water, carbon dioxide, inorganic compounds and new microbial cellular constituents.
The whole process depends entirely on nature's microorganisms - bacteria, fungi and yeast - to break down the hydrocarbon molecules of their substance. Some chemical structures, such as natural (vegetable) oils, are more susceptible to microbial breakdown than others and will biodegrade much faster than petroleum oils. Biodegradable vegetable based oils will typically completely biodegrade within a month or two, whereas most petroleum based products will typically biodegrade in the environment within two months to two years.
It is important to understand that there are two main types of designations for biodegradability; readily biodegradable and inherently biodegradable. For instant clarification, 'readily biodegradable' is the preferred option.
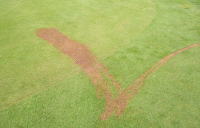
I apologise for the technicality of the following paragraphs, but it is also important to understand that there are two standards that are primarily used to determine biodegradability - the Coordinating European Council (CEC L-33-A-93) and the Organisation for Economic Cooperation and Development (OECD 301).
According to these tests, a fluid is readily biodegradable if it biodegrades more than 80% within twenty-one days, (CEC L-33-A-93), or more than 60% within twenty-eight days (OECD 301). This is the preferred type of fluid, as it will degrade before significant environmental damage has occurred and the affected area will require little in terms of long-term remedial renovation. Vegetable-based hydraulic fluids and some of the synthetic oils are considered readily biodegradable.
An inherently biodegradable fluid will degrade very slowly over a longer time; usually months to years. These types of fluids can exist in the environment for several years, continuing to cause substantial damage to turf and subterranean water and require long-term remedial work, due to their environmental persistence. Typically, these products are conventional petroleum-based lubricants.
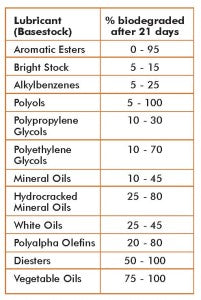
In future, a new test method for determining biodegradability of lubricants in natural environment (CEC-L-103-12) will be used.
Characteristics and Performance of Biofluids
The physical properties of biodegradable fluids differ from those of hydraulic fluids based on a mineral basestock. Their lubricating properties are superior to mineral basestock fluids as they have good anti-wear properties and a lower pour point.
Fluids made from vegetable oils and vegetable oil based synthetic esters are not water soluble. Their specific gravity, which is about 0.92 g/ml, makes them lighter than water but heavier than mineral oil products. In contrast to water soluble products, they are retained in the upper layers of the soil following an oil spillage.
Although vegetable based hydraulic fluids are sometimes regarded as having shorter life spans and less temperature resistance, they vary widely. Fluids made from virgin plant oils should be used in machines operating at temperatures between -10 °C and +70 °C, temperature excursions either side of these for short periods are not immediately detrimental to the performance of the biofluid.
However, at longer lasting or continuous high working temperatures, the molecular structure of vegetable oil will be damaged and deterioration or ageing of the fluid is drastically accelerated.
If an environmentally friendly product is required outside the common temperature range mentioned above, a biodegradable synthetic fluid would be required. These synthetically manufactured products still offer all the biodegradability of vegetable oils, but they can operate at temperatures in excess of +200°C and still retain a long fluid service life. The only caveat is that they tend to have a significantly higher price.
If a biodegradable fluid is not agitated for a considerable period of time, the surface in contact with air and/or moisture may start to biodegrade, which is what it is designed to do. This can have an impact on the way the fluid is stored; for example, in a used container or if a machine is stored and not used during the quieter winter period. To prevent this natural occurrence, it is suggested that the machinery stored during prolonged inactive periods is started and run for a few minutes once a month. Also, half-full containers should be given a vigorous shake at the same interval.
Ageing of Biofluids
Various possible causes can lead to irreversible and irreparable damage to hydraulic fluids in general, which can be regarded as ageing of the fluid. This deterioration occurs not only during use of the fluid, but also during storage. It may be accelerated by particulate and water contamination, as well as direct contact with metals.
It is widespread, but mistakenly, believed that mineral based hydraulic fluid does not age. There are chemical reactions in every type of oil, which change the properties of the base fluid, as well as the additive package. If a hydraulic fluid (or lubricant) cannot perform to its technical requirements, it has to be changed.
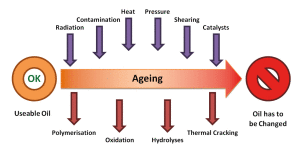
Polymerisation: This leads initially to an increase in viscosity and, eventually, to the formation of silt and sediment. This reaction is dependent on temperature, moisture, light and metallic catalysts. The result is an hydraulic system reacting and performing much slower than normal.
Oxidation: Oxidation is the loss of electrons or an increase in oxidation state of a molecule. If the oil comes into contact with oxygen, e.g. through the air breather of the reservoir, the oxygen will react primarily with the molecular double bonds of the oil. The more double bonds are present in the molecules, the faster the oil will oxidise. The final reaction products are often very corrosive, which can cause damage to machine components, especially to the seals, as well as silting of the oil.
Hydrolysis: The chemical reaction between an ester molecule (found in oils and lubricants) and a molecule of water or metal compound is described as hydrolysis or saponification (formation of soap), causing the cleavage of chemical bonds of the ester molecule into alcohol and acids. The acid products especially can lead to damage of the hydraulic system and its components.
Thermal Cracking: When the molecules of the oil are split by high temperatures it is called thermal cracking. The temperature spikes may be caused by cavitation, too small diameters of the hydraulic pipes or hoses, lubrication grooves, etc. Some of the reaction products are very flammable gasses, which will cause further temperature spikes during oxidisation, so that a chain reaction could be started.
To counteract this ageing process of oil, it is important to look after and maintain the oil. Research has proven that optimal filtration can extend the life of oil. Removal of metal particulates and oil ageing products will slow down the chain reactions and lengthen the intervals between necessary oil changes.
Types of Biofluids and their Applications
Due to mineral-based hydraulic oil's slow and long biodegradability, the use of vegetable-based hydraulic oil could be an excellent environmentally friendly alternative for the fine turf manager. Readily biodegradable hydraulic fluids are classified in the following four main groups, as dictated by DIN ISO 15280:
Conventional Vegetable-based Fluids - HETG (Hydraulic Oil Environmental Triglyceride): At the start of biofluid development, the focus was on lubricants made from vegetable oils, typically from rape or sunflower seeds. Vegetable-based fluids are readily biodegradable.
Unfortunately, multiple unsaturated fatty acids in the vegetable-base stock leads to oxidation and hydrolysis, especially at elevated temperatures. In general, these vegetable-based fluids can only withstand operating temperatures not exceeding 80°C. A further drawback is that they become unstable when exposed to wet environments or are contaminated with water.
Therefore, their performance is most suited to cool and dry operating conditions and equipment operators must take care to ensure that these limitations are not exceeded. These fluids are typically used in land-based and forestry machines, which are subjected to low peak performance only.
Synthetic Esters - HEES (Hydraulic Oil Environmental Ester Synthetic): The second phase of biofluid development focused on synthetic esters. Synthetic esters are readily biodegradable and only very slight water pollutant. Full-synthetic saturated esters exceed in oxidation tests, compatibility and lubricating properties in comparison to most mineral oils.
Esters are synthesised by the reaction of vegetable oil with fatty acid and alcohol, with water and heat as by-products. At elevated temperature, and in the presence of water, this reaction is reversible, which is known as hydrolysis. This reforms the alcohols, acids and original triglycerides. which can cause rust and wear, seal degradation and corrosion to yellow metals. Consequently, ester-based fluids must be maintained in a cool, dry state to obtain maximum performance. They are used where higher working temperature of the fluid cannot be avoided; such as construction machines (excavators).
PAO-based Fluids - HEPR (Hydraulic Oil Environmental Polyalphaolefine and Related Hydrocarbons): This classification embodies fluids blended from Polyalphaolefine (PAO) basestock and related hydrocarbons, such as bio-polyolefin. These are made by hydro cracking of the paraffins resulting from mineral oil distillation.
One distinct advantage of PAO-based fluids is that they can be tailor-made to fit specific requirements. These fluids do not hydrolyse and, as such, are much more stable in hot, wet conditions. Bio-olefins are typically compatible with Buna N, Viton and all common elastomers, as well as adhesives used in filters. One drawback is its high price and another is that it is only inherently biodegradable.
PAG-based Fluids - HEPG (Hydraulic Oil Environmental Polyglycole): PAGs can be either polyethylene or polypropylene oxide-based, with water solubility differing according to type and are produced from mineral oils. Polyethylene-based PAGs are highly water soluble, are poorly miscible with mineral oils and are very polar. Their water solubility helps to provide biodegradability. Their technical properties are on par with those of mineral oil. They are mainly used in hydro-engineering, such as sluices and movable bridges.
Lubrication manufacturers and blenders offer nowadays HETG and HEES products which are inherently ageing and oxidation resistant, maintain a good viscosity-temperature relation and are generally compatible with hydraulic components, including seals and O-rings.
The benefits of using a biodegradable hydraulic fluid are considerable should the fluid leak, but it should also be understood how biodegradability can impact an hydraulic fluid's performance. As stated previously, vegetable-based fluids are generally more readily biodegradable, but they will not provide comparable service life to that of a standard mineral hydraulic fluid. However, when compared to conventional, mineral-based fluids, synthetic-based fluids will likely offer extended service life, while also being more readily biodegradable.
Generally speaking, biodegradable oils should be maintained and monitored during use just like mineral-based oils. They must be kept cool, clean and dry (water-free) and their condition should be monitored on a regularly scheduled basis using readily available oil analysis techniques.
Little research has been published on turf damage to assess recovery from hydraulic fluid damage; even less on fine turf maintained at putting green or bowling green height.
M.L. Elliot and M. Prevatte published their research Comparison of Damage to 'Tifgreen' Bermudagrass by Petroleum and Vegetable Oil Hydraulic Fluids in the journal HortTechnology. In summary it stated:
"Petroleum and vegetable oil hydraulic fluids were spread on `Tifgreen' Bermudagrass at different volumes and different temperatures to simulate a turfgrass maintenance equipment leak. Initial damage, recovery, and effects for a 1-year period were compared among treatments.
All hydraulic fluid treatments resulted in 100% leaf necrosis (death of the plant cells) within 10 days of application. Turfgrass recovery was influenced primarily by the fluid volume. After recovery, only plots treated with petroleum hydraulic fluid were periodically chlorotic, (yellowing of the leaf due to lack of chlorophyll) resulting in lower turfgrass quality. Long-term negative effects of hydraulic leaks from golf course equipment may be reduced by using vegetable oil hydraulic fluid."
William L. Berndt published his research Effect of Synthetic Hydraulic Fluid on Warm-Season Turfgrass in the journal Applied Turfgrass Science. It can be summarised as:
"Synthetic hydraulic fluid was compared to traditional hydraulic oils for its potential to cause turf injury. Effects of fluid type, volume, and temperature on area of injury, percent necrosis, and time to healing were investigated at Edison College via experiments on hybrid Bermudagrass (Cynodon dactylon L. [Pers.] x C. Transvaalensis Burtt-Davey) or seashore Paspalum (Paspalum vaginatum O. Swartz).
Synthetic fluid caused minimal shoot necrosis that healed within 10 days, while hydraulic oils caused 100% necrosis of shoots. Synthetic fluid applied on putting greens in the field caused an average of 70 cm² of injury with 17% necrosis after 5 days. Time to healing was 15 to 30 days. In contrast, hydraulic oils caused larger areas of injury with more necrosis and longer healing times.
Compared to hydraulic oils, synthetic fluid consistently caused less injury to warm-season turfgrasses and is a viable replacement for traditional hydraulic oil in turf management equipment."
Roch Gaussoin of the University of Nebraska published his research Hydraulic oil spills: Reducing the damage in the journal Golf Course Management. It can be summarised as:
"Hydraulic oil spills have a disastrous effect on bentgrass golf greens. Depending on the type of oil used and the corrective action taken, recovery can occur within four weeks after the spill or take longer than two months. Prompt action, as well as the right choice in hydraulic oil, can significantly improve recovery."
What the above studies and field observations revealed is that grass and soil is allowed to regenerate more quickly after spills of biodegradable vegetable-based and synthetic hydraulic fluids, with no residual environments effects.
On the other hand, with conventional hydraulic fluids, leaks or spills can contaminate nearby soil and groundwater. Re-seeding and germination of new grasses were not noticeably affected by contamination in the soil. However, the single best approach to protecting the environment, as well as mowing equipment and operations, is to prevent leaks and spills through good routine maintenance.
Should a leak or spill occur, the quicker remedial action is taken, the quicker and better recovery will occur. To improve recovery, it is suggested that the spilled area is treated with a liquid dishwashing detergent and flushed with water within twenty minutes of the spill. This treatment will disperse the hydraulic oil and reduce the severity of the damage, but be aware that it also can spread the problem over a slightly larger area.
Other treatments have been tested and applied, such as activated charcoal, calcined clay, granular dishwashing detergent, waterless skin cleaner and a non-ionic wetting agent and water. It has been reported that activated charcoal will absorb oil from spills, but will not increase breakdown, resulting in an unsightly, messy black residue within the damaged turf.
Other products, such as oil emulsifiers and synthetic absorbents, are also available to alleviate damage caused by hydraulic fluid spills. Liquid dishwasher detergent was still the best corrective treatment.
Any of these techniques may help to reduce the severity of the damage, especially on longer turf. However, on greens, it is imperative to get a quick repair to maintain playability. For this, the above-mentioned techniques may be of limited value, depending on the location of the damage. Re-turfing or plugging can repair the area quickly and return it to play as soon as possible.
Without re-turfing, a hydraulic leak on a Creeping Bentgrass or Bentgrass/Poa Annua green will take four to six weeks to heal. On Bermudagrass, healing actually may be more rapid without re-turfing. However, playability will still be affected for a longer period.
The last option for repair is to overseed and topdress the affected area to promote healing. All the above studies indicated that seed germination was not impacted by oil residual. The biggest problem with this approach is the downtime that it requires. Small or out-of-play areas can easily be corrected by overseeding.
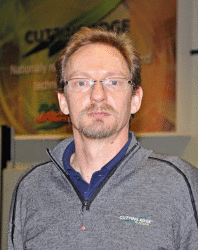
If turf or plugs are used to repair the spilled area, frequent, light topdressing will help to smooth the affected surface. Turfed areas may need to be watered two or three times daily depending on weather conditions.
Conclusion
Even with the best maintenance programme, there is still potential for a hydraulic fluid or lubricant spill, which is why a vegetable-based readily biodegradable or a synthetic-based hydraulic fluid in the turf maintenance machines could be a significant advantage.
The damaged area will recover after a spill much quicker, provided it is treated correctly and quickly. There is also no environmental impact, neither in the soil, nor in nearby open or subterranean waters.